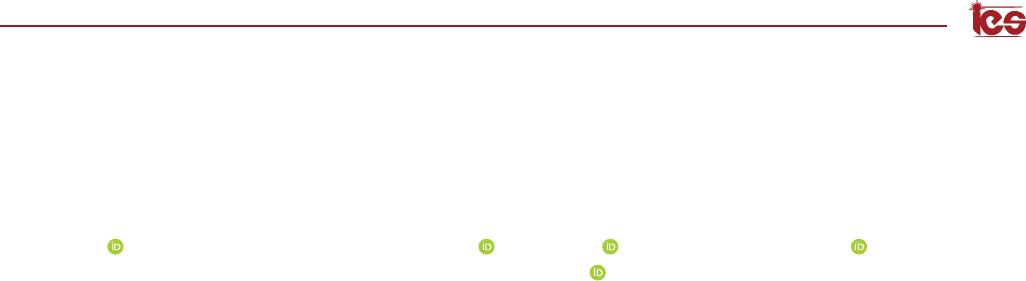
7862 IEEE TRANSACTIONS ON INDUSTRIAL INFORMATICS, VOL. 20, NO. 5, MAY 2024
Graph Convolutional Neural Network for
Intelligent Fault Diagnosis of Machines
via Knowledge Graph
Zehui Mao , Senior Member, IEEE, Huan Wang , Bin Jiang , Fellow, IEEE, Juan Xu , Member, IEEE,
and Huifeng Guo
Abstract—Considering the challenge of deep mining of
root causes in machine failures, a knowledge aggrega-
tion fault diagnosis (KAFD) model is proposed, in which
the graph convolutional network (GCN) GraphSAGE is im-
proved and introduced into the knowledge graph (KG)-
based fault diagnosis. Historical maintenance data of ma-
chines is used to construct a fault phenomenon-FBG,
which is then combined with the fault diagnosis knowledge
graph (FDKG) to form a collaborative FDKG. A single-layer
knowledge aggregation network (KAN) that incorporates
sensitivity factors and configures different types of GCN
aggregators is constructed in the proposed KAFD. Based
on deep neighbor aggregation operations on collaborative
FDKG, KAFD obtained by stacking multiple KANs, can cap-
ture the higher order structural information and semantic
information, which results in the multihop reasoning, im-
provement of the rationality and diversity of fault cause
tracing. The KAFD is experimentally validated through two
fault diagnosis datasets, which are constructed by the
maintenance data of an industrial enterprise, and the re-
sults demonstrate the excellent performance.
Index Terms—Fault diagnosis, graph neural networks,
industrial machines, knowledge graph (KG).
I. INTRODUCTION
I
NDUSTRIAL machines have been becoming more complex
and expensive with the high performance, as the advanced
intelligent devices and monitoring technologies are introduced
Manuscript received 23 October 2023; revised 10 December 2023;
accepted 6 February 2024. Date of publication 29 February 2024; date
of current version 6 May 2024. This work was supported in part by the
National Key Research and Development Program of China under Grant
2021YFB3301300 and in part by ZTE Industry-University-Institute Co-
operation Funds. Paper no. TII-23-3628. (Corresponding author: Juan
Xu.)
Zehui Mao, Huan Wang, and Bin Jiang are with the College of
Automation Engineering, Nanjing University of Aeronautics and As-
tronautics, Nanjing 210016, China (e-mail: zehuimao@nuaa.edu.cn;
wanghuan233@nuaa.edu.cn; binjiang@nuaa.edu.cn).
Juan Xu is with the College of Computer Science and Technology,
Nanjing University of Aeronautics and Astronautics, Nanjing 210016,
China (e-mail: juanxu@nuaa.edu.cn).
Huifeng Guo is with the State Key Laboratory of Mobile Network and
Mobile Multimedia Technology, Shenzhen 518000, China, and also with
the ZTE Corporation, Shenzhen 518000, China (e-mail: guo.huifeng2
@zte.com.cn).
Color versions of one or more figures in this article are available at
https://doi.org/10.1109/TII.2024.3367010.
Digital Object Identifier 10.1109/TII.2024.3367010
into them. However, this leads to an increasing requirement on
reliability and safety of industrial machines subjected to faults
and failures [1]. Fault diagnosis that detects the occurrence of a
fault as early as possible and identifies the location and type of
the fault as accurately as possible, is a key mean to ensure the
safety of industrial machines [2], [3].
With the development of technology, the fault diagnosis
methods are receiving more and more attention, including the
model-based methods [4], [5], data driven-based methods [6],
[7], [8], [9], and knowledge-based methods [10]. As a significant
amount of maintenance records can be accumulated during the
long-term maintenance and repair processes of industrial ma-
chines, which contain the valuable knowledge and information
related to machine fault diagnosis.
Knowledge-based fault diagnosis methods commonly include
expert systems, fault tree analysis, and knowledge graphs (KGs).
By automating the acquisition, organization, and analysis of
various machine information, including maintenance history and
expert experience, KG-based fault diagnosis methods can iden-
tify fault root causes and provide solutions. Existing research
mainly utilizes KG reasoning techniques [11], [12], [13], which
can make inferences about potential causes or solutions based
on entities and relations. During the machine operating, the
new data and information reflecting new faults often emerge
often generates. Incorporating new data and information into
existing KGs and reasoning requires offline updates, difficult to
be updated and improved dynamically.
Recommendation systems, by continuously collecting feed-
back from maintenance personnel during the maintenance pro-
cess, can achieve dynamic updates and continuously improve
the accuracy of fault cause recommendations, addressing the
issue of dynamic updates in KG-based fault diagnosis. Fusing
the KGs and recommendation algorithms can address the issue
of dynamic updates in KG-based fault diagnosis, which can be
primarily achieved through the propagation-based methods [14],
[15]. Propagation-based methods can expand the depth of infor-
mation reception by following the deep aggregation, thereby
fully utilizing the information in the KG to better predict fault
causes and locate potential fault causes. Deep aggregation is
the core of graph convolutional neural networks (GCN) [16],in
which GraphSAGE [17] is a representative model. But GCNs
like GraphSAGE is not feasible for weighted graphs, as they
can only perform equally weighted aggregations of neighboring
1551-3203 © 2024 IEEE. Personal use is permitted, but republication/redistribution requires IEEE permission.
See https://www.ieee.org/publications/rights/index.html for more information.
Authorized licensed use limited to: ZTE CORPORATION. Downloaded on November 26,2024 at 06:05:55 UTC from IEEE Xplore. Restrictions apply.
文档被以下合辑收录
相关文档
评论